Approximately 90% of all structural building failures are caused by moisture. With the exception of the homeowner, moisture is the #1 enemy of the house. Unfortunately, moisture damage typically occurs in concealed spaces. This makes it difficult for most home inspectors to identify.
Good inspectors know there are 3 major elements that impact the risk of moisture intrusion.
- The more complex the design of the home the higher the risk.
- Poor drainage of water on or around the house increases the danger.
- Missing or improper flashing details can be a disaster.
Based upon the analysis of these 3 principles, an experienced inspector will determine whether the probability of concealed moisture damage is low, medium, or high. Regardless of what other ‘experts’ may say, home inspectors are required to communicate these observations to our client and make the appropriate recommendation.
Let me give you an example. Within the last year I inspected an Italian Renaissance home with an elaborate and complicated building design. This building included numerous room projections from the main structure, a 3rd level tower, and a traditional stucco exterior finish.
A flat roof deck was incorporated within the main hip roof structure that included a large skylight and an internal drainage system.
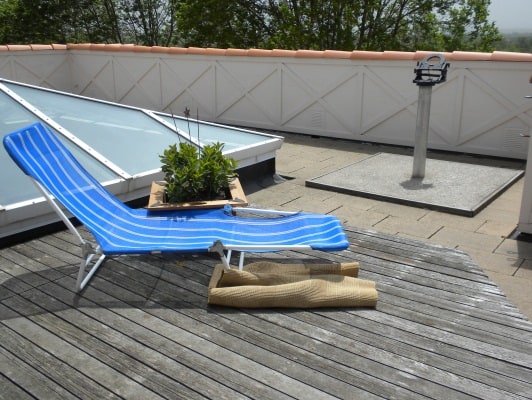
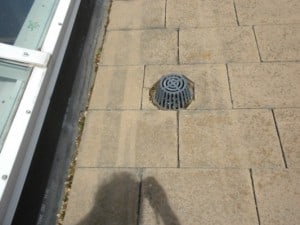
The perimeter of all windows, doors, band boards, and corners had ‘bump out’ projections without any flashing. Doors onto the flat roofs were level with the deck and had no room for threshold flashing. The stucco was extended below grade without any drip screed flashing. And the roof did not include kickout flashing.
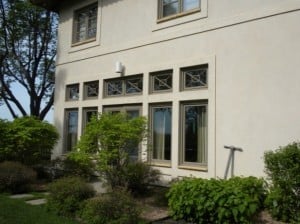
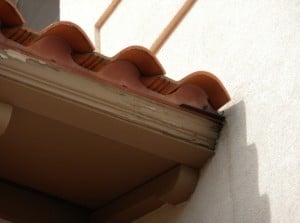
Seemed like a no brainer…complex house design, poor roof drainage, and missing flashing details made this high risk. However, the home had been previously moisture tested by a very reputable contractor. The infra-red imaging and meter probing results were all negative. The ‘expert’ concluded no to low probability of moisture intrusion.
Should a professional home inspector change their conclusion and recommendation? Absolutely not, go with what you know. In this example my clients relied upon the moisture testing, moved into the home and quickly discovered the exterior wall structure was rotted out, the house was unsafe to live in and would require over a half a million dollars to fix.
Always remember…STAY WITH WHAT YOU KNOW…an inspector is paid for their opinion not someone else’s.
Doug Hastings
MN Home Inspector, Minneapolis & St. Paul
ASHI Certified Inspector, ACI
Kaplan University, Home Inspection Lead Instructor
Visit and ‘Like’ our Cities Inspection Facebook page for more home updates.